Бережливое производство на КЭАЗ: философия и успешные кейсы
5 июня 2023 года
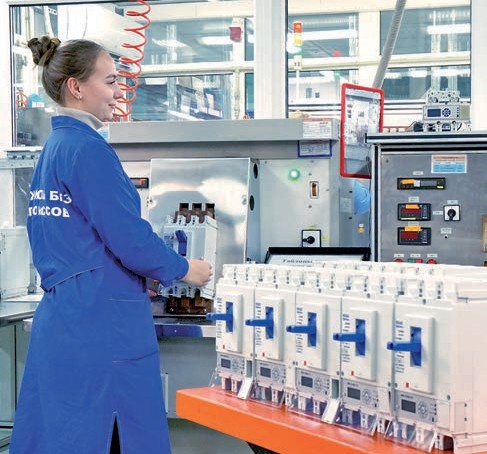
КЭАЗ — ведущий российский производитель и разработчик электротехники с богатой историей и обширным производственным опытом. Компания отличается полным циклом производства, аппараты изготавливает из собственных комплектующих, а также обеспечивает все этапы послепродажного обслуживания. И чтобы выпускать оборудование для решений «под ключ», требуется произвести тысячи операций в день. Сократить потери и повысить эффективность предприятию помог проект повышения производительности труда, к которому КЭАЗ подключился в 2020 году, при этом отдельные элементы бережливого производства внедрялись с 2014 года. Сегодня компания готова поделиться опытом и рассказать, как повысить производительность по отдельным линейкам продукции на 30 и более процентов, а также как мотивировать к эффективному результату каждого сотрудника.
30% за 4 года
Повысить производительность на 30% к 2024 году и уйти от потерь, которые не приносят добавленной стоимости продукта. Такую цель поставили перед собой на предприятии с первых дней участия в нацпроекте «Повышение производительности труда и поддержка занятости». Под руководством опытных тренеров из Федерального центра компетенций в компании стали постепенно снижать время протекания процессов, уменьшать объем незавершенного производства и, за счет этого, увеличивать выработку.
— Участие в проекте позволило нашей компании вывести внедрение бережливого производства на новый уровень. Благодаря активной работе консультантов у сотрудников компании появился практический опыт использования картирования для повышения эффективности производственных процессов компании. Также хороших результатов удалось достичь при применении SMED и сбалансированной работы, — отмечает директор по развитию производственной системы КЭАЗ Александр Потапов.
В качестве пилотного выбрали участки, на которых изготавливают детали, узлы и осуществляют сборку автоматических выключателей OptiMat D — флагманской серии оборудования.
На первых этапах внедрением программы занимались около 30 человек — в команду вошли мастера участков, технологи, руководители производственных подразделений. При том, что в компании работают более 2000 сотрудников, нам пришлось провести масштабную работу, в том числе и для формирования «бережливого мышления» у наших специалистов.
— Мы использовали целый спектр инструментов — среди них были картирование, стандартизированная работа, быстрая переналадка, выравнивание, — делится Александр Потапов. — В результате удалось обнаружить и предотвратить некоторые потери — например, лишние перемещения деталей и узлов, пролеживания, или лишние действия в подготовительных и заключительных операциях, при переналадке.
Компания поставила себе амбициозные задачи — сократить время протекания процессов на 25 %, сократить НПЗ на 33% и повысить производительность на 25 %. Основной положительный эффект достигли за счет сокращения времени переналадки на участке прессов со штампами последовательного действия. В глобальном смысле это позволило компании выпускать более широкий ассортимент деталей, а так как переналадка станков происходила быстрее — мы смогли, при необходимости, производить небольшие партии деталей.
Еще одна задача, которую успешно решила компания, — доработка некоторых штампов и пресс-форм. Это позволило уйти от дополнительной ручной обработки деталей и автоматизировать процесс. Эффект не заставил себя ждать — сократилось время пролеживания деталей, процент несоответствующей продукции, лишняя транспортировка. Это в свою
очередь положительно повлияло на скорость выпуска продукции.
На практике внедрение инструментов бережливого производства позволило повысить производительность труда при изготовлении группы продуктов OptiМat D на 22 %, сократить время переналадки на участке до 68%. В результате предприятие снизило объем незавершенной продукции и повысило свою гибкость и эффективность. Поэтому в кризисный 2022-й год удалось не только сохранить, но и увеличить объем производства. Оптимизация, которой удалось добиться в рамках проекта, помогла быстро адаптироваться к новым условиям и заполнить ниши ушедших западных компаний. Важно, что коснулась оптимизация только процессов, а штат сотрудников, наоборот, пополняется в связи с ростом производственных мощностей.
Здесь нужны стайеры
Инструменты бережливого производства важно не только внедрить, но и не дать этому процессу угаснуть. Здесь многое зависит от настроя каждого из сотрудников. У многих компаний возникают трудности на этом этапе, но КЭАЗ выработал собственную тактику.
— Есть басня Лафонтена «Заяц и черепаха», многие в детстве ее читали. Так вот внедрение бережливого производства требует подхода черепахи. Здесь нужны не спринтеры, а стайеры, которые каждый день занимаются внедрением инструментов, взаимодействуя с сотрудниками, каждый день объясняют, в чем преимущество данного инструмента и что его внедрение даст данному сотруднику, — делится Александр Потапов. — Нужно каждый день выходить в гембу, разговаривать с сотрудниками, самому смотреть на оборудование, оснастку, детали и узлы, чтобы понимать, в чем проблема, и какие пути решения нужно применить для сдерживающих и корректирующих мероприятий.
На предприятии хорошо зарекомендовал себя инструмент 5С. Эти пять шагов вводят для персонала привычку четко следовать правилам, а также помогают оптимизировать рабочее пространство. В результате каждый сотрудник видит, что инструменты бережливого производства приносят пользу именно ему. Но и на этом этапе возможны сложности.
— На мой взгляд, наша ментальность не предполагает четкого выполнения правил. Если японцу сказали, как именно нужно делать данное действие, он и будет его делать именно так. Наш народ более креативный, в результате появляется несколько вариантов выполнения процессов, что хорошо для ремесленной мастерской, но плохо для предприятия, которое выпускает серийную продукцию. Именно поэтому я и советую компаниям, которые только становятся на путь бережливого производства, начинать с 5С. Эта система приучает сотрудников выполнять правила, — считает директор по развитию производственной системы Александр Потапов. Еще один секрет успеха — постоянная работа с наставниками. На КЭАЗ достаточно высокий уровень внедрения инструментов бережливого производства, но компания продолжает привлекать консультантов. Сейчас в работе проект «Эволюция производственной системы», в котором принимают участие бывшие сотрудники «Тойоты». Их опыт позволяет посмотреть на производственные процессы по-новому и найти точки роста. КЭАЗ постоянно использует в работе принцип PDCA «планирование — реализация — анализ — корректировка».
Новое мышление
Говорить с сотрудниками на одном языке — важно, но более ценно получать обратную связь. Около года назад на КЭАЗ запустили систему подачи предложений по улучшениям — кайдзен (ППУ).
Кайдзен — концепция менеджмента, основанная на постоянном улучшении процесса работы, от директора до рядового рабочего. Цель кайдзен — производство без потерь.
Каждый сотрудник компании может в простой форме представить предложение, которое касается оптимизации рабочего места, повышения качества продукции или снижения ее себестоимости.
Сотрудники получают 15% от полученной экономии после внедрения улучшения. В прошлом году удалось собрать около 2000 предложений от персонала и достичь потенциального экономического эффекта более 6 млн руб.
Большинство предложений касаются эргономики и безопасности рабочих мест. Сейчас сделан акцент на технологических процессах.
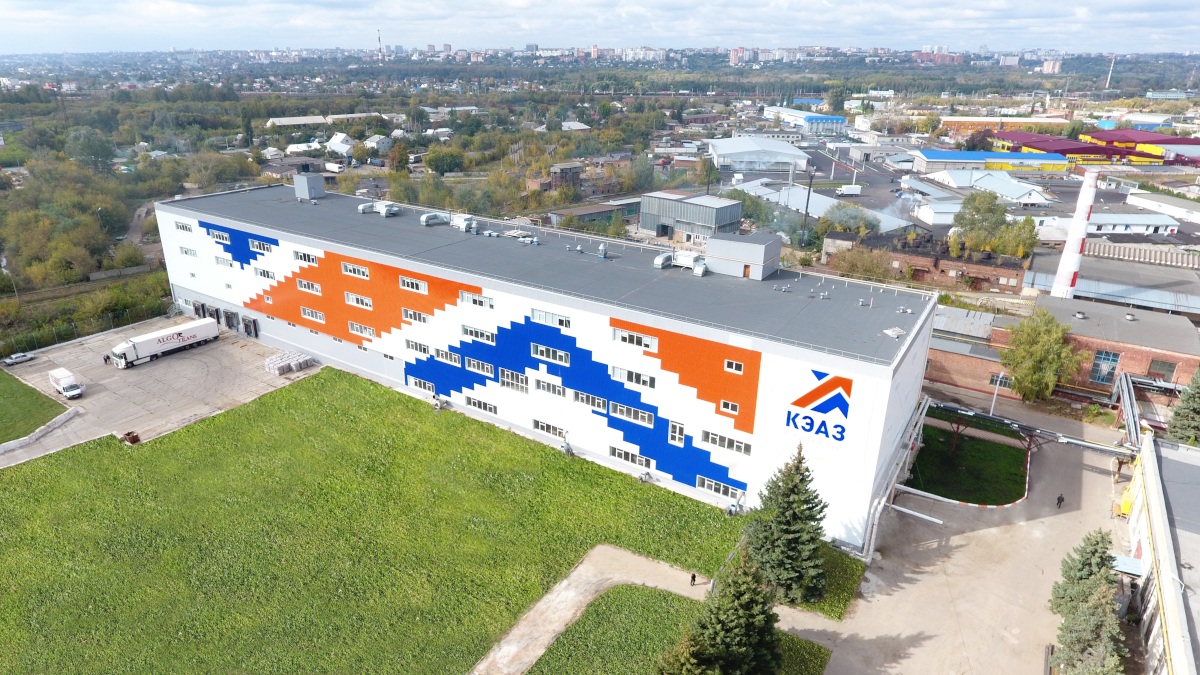
— Такая позиция позволяет уйти от равнодушия персонала и дает возможность использовать активность и интеллект каждого сотрудника. Организация становится саморазвивающейся и постоянно адаптируется к изменениям, — уверен директор по производству КЭАЗ Сергей Токин. — Часто процессы, которые были оптимальны вчера, сегодня уже таковыми не являются. Именно поэтому нужно постоянно вовлекать персонал в работу по внедрению улучшений. Никто кроме самого сотрудника не знает лучше рабочее место и выполняемую им операцию. Именно он видит, эффективна его деятельность или нет, и может предложить варианты повышения ее эффективности. Постепенно бережливая культура захватывает все производственные процессы. Эта философия активно внедряется и в офисных подразделениях КЭАЗ. Активно работают информационные центры. Там с сотрудниками обсуждают планы, акцентируют внимание на проблемах, ставят задачи по кайдзен. Сейчас запускается проект, связанный с внедрением всеобщего обслуживания оборудования. Задача — получить объективный показатель ОЕЕ по ключевому оборудованию не меньше 95%. Успешные кейсы сотрудников КЭАЗ КЭАЗ практикует тактику «маленьких шагов», то есть совершенствуется в мелочах. Сотрудники предприятия активно предлагают ППУ — предложения по улучшению производства, которые помимо повышения мотивации сотрудников, помогают оптимизировать процессы и имеют экономический эффект.
1. Работа с Гидравлическим прессом в цехе пластмассовых изделий.
Для качественной работы станка из его бункера нужно удалять отходы. Раньше это делали вручную, работа была долгой и неудобной для прессовщика. Сейчас станок усовершенствовали, и для удаления шлака используют вакуумные пистолеты. Это улучшило эргономику рабочих мест и позволило ускорить процесс очистки.
2. Апгрейд роликовых ножниц.
За счет применения средств малой автоматизации (шуруповерт, стеллажи на колесах) удалось сократить время переналадки роликовых ножниц на 50%. Раньше этот рабочий центр был сильно загружен, и сотрудникам приходилось задерживаться на работе, чтобы выполнить производственные задания. Сейчас таких проблем нет.
3. Шахтная VS камерная печь.
Это предложение обеспечило экономический эффект в десятки тысяч рублей. Сотрудники термического отделения посоветовали изменить технологию закалки деталей. Вместо камерной печи с небольшим объемом загрузки, они предложили использовать шахтную печь. В результате производительность труда на данной операции повысилась в разы.
Готовы внедрять лучшие практики
Благодаря проекту повышения производительности труда сотрудники предприятия обучились новым инструментам бережливого производства, внедрение которых помогло повысить производительность труда, сократить время протекания процессов и снизить незавершенку. Кроме этого, была запущена система обучения, которая позволяет дать сотруднику навыки использования этих инструментов с первых дней присутствия на предприятии.
— Наша компания является открытой, мы с удовольствием делимся своими знаниями и достижениями. К нам постоянно приезжают делегации, и мы с удовольствием проводим экскурсии. Многие гости задают интересные вопросы, благодаря которым мы улучшаем наши процессы. Также мы сами посещаем другие компании, чтобы подсмотреть лучшие практики и внедрить их у себя, — отмечает управляющий директор производственно-технического блока КЭАЗ Дмитрий Коробка.
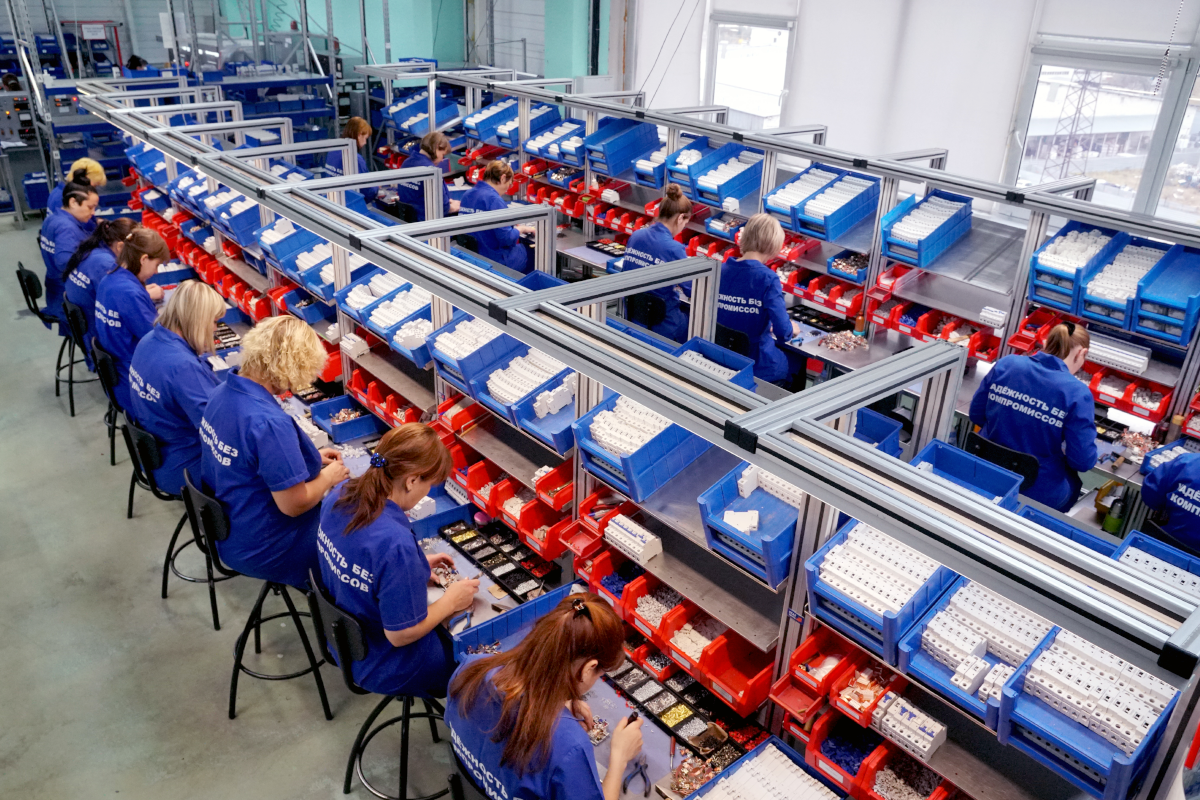
Альманах "Управление производством"
Мая, 2023
Последние новости
- По следам ПМЭФ - КЭАЗ стал частью особой экономической зоны Санкт-Петербурга 26 июля
- Александр Хинштейн посетил производство КЭАЗ в промтехнопарке «СОЮЗ» 18 июля
- КЭАЗ стал лауреатом промышленной премии "Индустрия" 8 июля
- "Ключ от сердца города" передал председатель совета директоров группы компаний КЭАЗ Андрей Канунников врио губернатора Курской области Александру Хинштейну 7 июля
- «Накопленный за 80 лет уровень экспертизы позволяет нам стать лидерами отрасли» 18 июня
Исправление орфографических ошибок
Если Вы заметили на сайте опечатку или неточность, мы будем признательны, если Вы сообщите об этом.
Выделите текст, который по Вашему мнению содержит ошибку, и нажмите на клавиатуре комбинацию клавиш: Ctrl + Enter